Sheet metal might not be the first thing that comes to mind when thinking about modern manufacturing, but it plays a crucial role. From cars to buildings, sheet metal is everywhere, providing strength and versatility. Understanding this material can unlock endless possibilities for various industries.
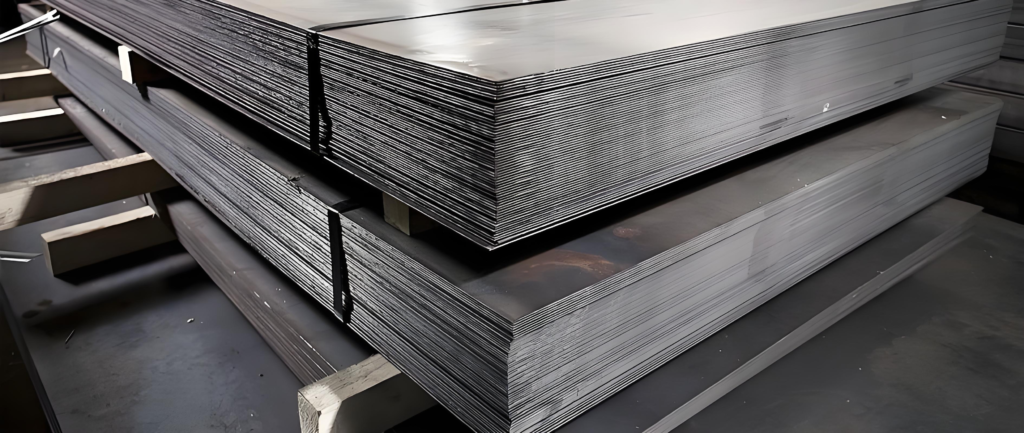
Properties of Sheet Metal: A Deep Dive
Material Composition: Steel, Aluminum, Stainless Steel, etc.
Sheet metal can be made from different materials, each offering unique benefits:
- Steel: Strong and widely available. It’s great for structural support.
- Aluminum: Lightweight and corrosion-resistant, perfect for industries where weight matters.
- Stainless Steel: Known for its durability and resistance to rust, making it ideal for kitchen equipment and medical tools.
Choosing the right material is vital based on the project’s needs.
Gauge and Thickness: Impact on Application and Strength
The gauge of sheet metal refers to its thickness. A lower gauge number means a thicker sheet. For example:
- 22 gauge: About 0.030 inches thick. Suitable for light applications.
- 14 gauge: About 0.075 inches thick. Good for applications requiring more strength.
Understanding gauge helps determine the right fit for specific uses.
Mechanical Properties: Tensile Strength, Yield Strength, and More
Mechanical properties are key indicators of a sheet metal’s performance. Key terms include:
- Tensile Strength: Maximum stress a material can withstand while being stretched.
- Yield Strength: The point at which the material starts to deform permanently.
These properties dictate how the metal will behave under stress.
Diverse Applications of Sheet Metal Across Industries
Automotive: Body Panels, Chassis Components, Etc.
In the automotive industry, sheet metal forms the backbone of design. Cars rely on it for body panels and structural components.
Construction: Roofing, Cladding, HVAC Systems, Etc.
Sheet metal is essential in construction for roofing, siding, and HVAC systems. It provides protection from the elements and enhances energy efficiency.
Electronics: Enclosures, Housings, Heat Sinks, Etc.
In electronics, sheet metal shields sensitive components from electromagnetic interference and helps manage heat dissipation. Products like computer cases and heat sinks are perfect examples.
Sheet Metal Fabrication Techniques: A Comprehensive Overview
Cutting Methods: Laser Cutting, Waterjet Cutting, Shearing, Punching
Fabrication starts with cutting. Common methods include:
- Laser Cutting: Precision cutting using lasers for intricate designs.
- Waterjet Cutting: Uses high-pressure water mixed with abrasives. Ideal for thick materials.
- Shearing: A quicker method for making straight cuts.
- Punching: Creates holes and shapes in sheets.
Choosing the right method depends on the design and material.
Forming Methods: Bending, Rolling, Stamping, Drawing
After cutting, forming shapes the metal. Techniques used are:
- Bending: Changes the angle of the sheet.
- Rolling: Shapes the metal into curves or cylinders.
- Stamping: Imprints designs or shapes into the metal.
- Drawing: Converts flat sheets into three-dimensional shapes.
These methods are vital for achieving specific designs.
Finishing Methods: Powder Coating, Painting, Plating
Finishing protects the metal and provides aesthetic appeal. Common techniques include:
- Powder Coating: Durable and colorful, perfect for outdoor products.
- Painting: Offers a smooth finish and can be done with various colors.
- Plating: Adds a thin layer of metal for protection and appearance, like gold plating.
Finishing can enhance the product’s lifespan.
Choosing the Right Sheet Metal for Your Project
Matching Material Properties to Application Requirements
Selecting the correct metal hinges on understanding the project’s requirements. Factors include:
- Strength needs
- Environmental exposure
- Weight limitations
Cost Considerations and Material Selection Trade-offs
Cost plays a pivotal role in material choice. Balance quality and budget carefully. Sometimes, a cheaper material can lead to increased costs down the road due to repairs or replacements.
Sourcing Sheet Metal: Suppliers, Distributors, and Considerations for Quality Control
Finding reliable suppliers is crucial. Look for:
- Certifications and quality standards.
- Customer reviews and ratings.
- Proximity to your location to reduce shipping costs.
Safety and Best Practices in Sheet Metal Handling and Fabrication
Personal Protective Equipment (PPE): Essential Safety Measures
Safety is non-negotiable. Workers should wear:
- Safety glasses
- Gloves
- Steel-toe boots
These protect against sharp edges and flying debris.
Handling and Storage: Safe Practices to Prevent Damage and Accidents
Proper handling ensures longevity. Store sheet metal on flat surfaces and avoid stacking to prevent warping.
Common Hazards and Mitigation Strategies
Awareness of potential hazards is essential. Common risks include:
- Sharp edges causing cuts.
- Heavy sheets leading to crush injuries.
Mitigate these by using tools and following safety protocols.
Harnessing the Power of Sheet Metal
Sheet metal stands as a versatile and critical material across various industries. Its properties enable diverse applications, while fabrication techniques enhance functionality. As technology advances, innovations will keep pushing the boundaries of what can be achieved with sheet metal.
Dive deeper into this fascinating world and consider how you can utilize sheet metal in your projects for greater efficiency and creativity.
Comments are closed