Main Characteristics and Selection of Common China Aluminum Alloy Grades
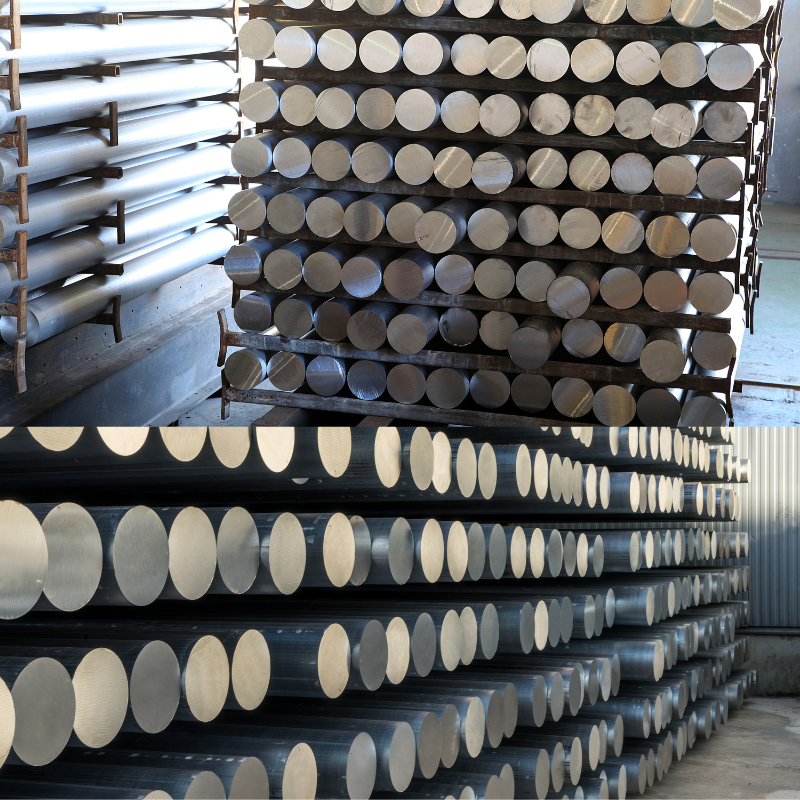
ZL101 is characterized by simple composition, easy melting and casting, good casting performance, good airtightness, welding and cutting performance is also relatively good, but the mechanical properties are not high. Suitable for casting thin-walled, large and complex shape, strength requirements are not high for a variety of parts, such as pump shells, gear boxes, instrument shells (frames) and home appliances on the parts. Mainly using sand casting and metal casting.
Zl101A is based on ZL101 with a trace amount of Ti, refining the grain, strengthening the alloy structure, its comprehensive performance is higher than Zl101, ZL102, and has better corrosion resistance, can be used as a general load of engineering structural parts and motorcycle, automobile, home appliances, instrument products on the various structural parts of quality castings. Its use is now second only to ZL102. Sand and metal mould casting are used.
Zl104 because of its large amount of working crystal, and added Mn, offset the harmful effect of Fe mixed in the material, has good casting performance and excellent air tightness, corrosion resistance, welding and cutting performance is also better, but the heat resistance is poor, suitable for the production of complex shape, large size and large load of power structural parts, such as supercharger shell, cylinder head, cylinder liner and other parts. etc. Mainly with die casting, but also the use of sand and metal casting.
Zl105, ZL105A due to the addition of Cu, reducing the content of Si, its casting performance and welding performance are worse than ZL104, but the room temperature and high temperature strength, cutting and machining performance are better than ZL104, plasticity is slightly lower, corrosion resistance is worse. Suitable for use as a complex shape, large size, there are heavy loads of power structural parts. Such as supercharger shell, cylinder head, cylinder liner and other parts. Zl105A is to reduce the content of ZL105 impurity element Fe, improve the strength of the alloy, with better mechanical properties than ZL105, more than casting quality castings.
ZL106 due to improve the content of Si, and added a trace of Ti, Mn, so that the alloy casting and high-temperature performance is better than ZL105, its airtightness and corrosion resistance is also better, can be used as a general load of structural components and better requirements of airtightness and work at higher temperatures in the parts, mainly using sand and metal casting.
ZL107 has excellent casting performance and airtightness, good mechanical properties, average welding and cutting performance, slightly poor corrosion resistance, suitable for making structural parts that bear general dynamic loads or static loads and parts with airtightness requirements. Sand casting is often used.
ZL108 has a high Si content and Mg, Cu and Mn are added, which makes the alloy have excellent casting performance, small thermal expansion coefficient, good wear resistance, high strength and good heat resistance. But the corrosion resistance is slightly lower. It is suitable for making pistons of internal combustion engines and other parts that require wear resistance and parts that require stable size and volume. It is mainly made of die casting and metal mold casting, and sand casting can also be used.
ZL109 is a complex alloyed Al-Si-Cu-Mg-Ni alloy. Due to the increase in Si content and the addition of Ni, the alloy has excellent casting performance and airtightness as well as higher temperature strength, wear and corrosion resistance are also improved, and the linear expansion coefficient and density are also greatly reduced. It is suitable for making internal combustion engine pistons and parts that require wear resistance and stable size and volume. It is mainly used for metal mold casting and sand casting.
ZL111 is a complex alloy. Due to the addition of Mn and Ti, the alloy has excellent casting properties, good corrosion resistance, air tightness, and high strength. Its welding and cutting performance is average. It is suitable for casting power structural parts with complex shapes and heavy loads (such as structural parts for aircraft engineer, water pumps, oil pumps, impellers, etc.), parts that require good air tightness and work at higher temperatures. It is mainly cast by metal and sand mould, and can also be cast by die casting.
ZL111 is a complex alloy. Due to the addition of Mn and Ti, the alloy has excellent casting properties, good corrosion resistance, air tightness, and high strength. Its welding and cutting performance is average. It is suitable for casting power structural parts with complex shapes and heavy loads (such as structural parts for aircraft engineer, water pumps, oil pumps, impellers, etc.), parts that require good air tightness and work at higher temperatures. It is mainly cast by metal and sand mould, and can also be cast by die casting.
ZL115: It has good casting performance and high mechanical properties. It is mainly used for heavy-load engineering structural parts and other parts, such as valve housings, impellers, etc. It is mainly cast in sand and metal mould.
ZL116: Because Zn and Sb in ZL115 alloy are removed and Ti and Be are added, the grain of the alloy is refined, and the harmful effect of Fe is reduced, so that the alloy has better casting performance, airtight performance and higher mechanical properties. It is suitable for casting power structural parts that bear large loads, such as some parts on aircraft, missiles and various parts requiring better comprehensive performance on civilian supplies. Mainly sand and metal mould casting.
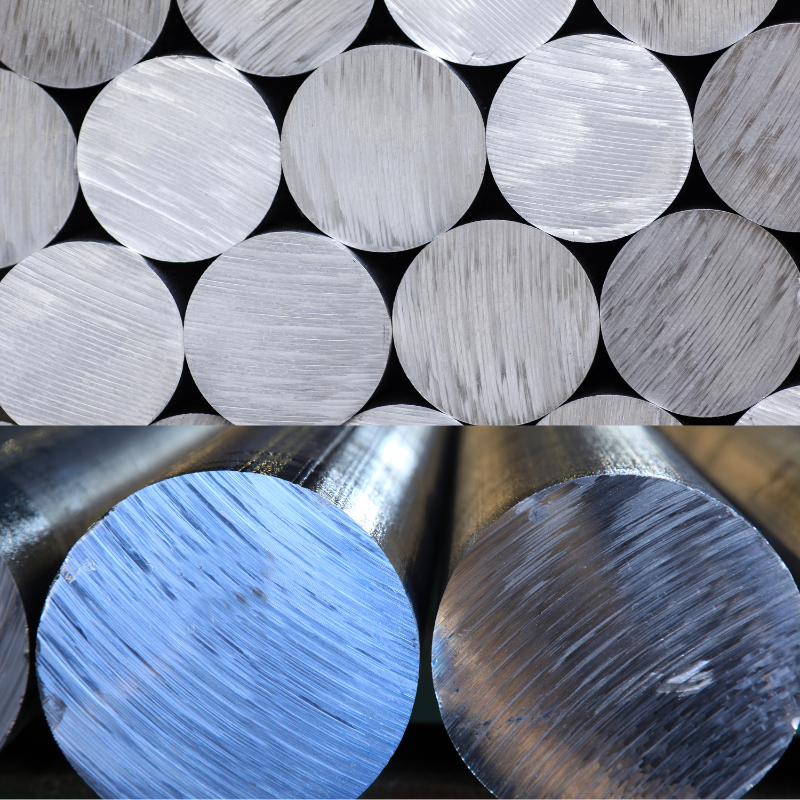
ZL117 alloy is a complex alloyed Al-Cu-Mg hypereutectic wear-resistant alloy. Because of its Si content of 19-22%, and the addition of trace elements Mn and rare earth elements RE, the alloy becomes a high-grade wear-resistant material with many primary Si particles with high hardness distributed on a soft matrix, and has good casting properties, good room temperature and high temperature strength, and low thermal expansion coefficient. It is suitable for casting internal combustion engine pistons, brake pads and other structural parts that require wear resistance, stable size and volume, and high strength. It is mainly metal casting , and can also be sand casting.
ZL201 has good room temperature and high temperature mechanical properties, general plasticity, general welding and cutting performance, but poor fluidity, thermal cracking tendency, poor corrosion resistance, suitable for casting structural parts working at higher temperatures (200-300℃) or parts bearing large dynamic or static loads at room temperature, as well as parts working at low temperatures (-70℃). Sand casting is often used.
ZL201A: This alloy greatly reduces the content of impurities Fe and Si, and has higher room temperature and high temperature mechanical properties than ZL201. It has good cutting and welding properties, but poor casting properties. It can be used for parts working at 300℃ or parts that bear large dynamic or static loads at room temperature. It is mostly used for sand casting.
ZL202 has good casting performance and high temperature strength, hardness and wear resistance, but poor corrosion resistance. It is suitable for casting parts with working temperature of 250℃ and small load, such as cylinder heads. It is mainly used for sand and metal casting.
Since ZL203 has a lower Si content, its fluidity is slightly poor, its thermal cracking tendency is greater, and its corrosion resistance is relatively poor, but it has good high temperature strength and welding and cutting performance. It is suitable for casting parts with a working temperature below 250°C and a small load and parts with a large load at room temperature, such as instrument parts, crankcases, etc. It is mostly used for sand casting and low-pressure casting.
ZL204A: This is a high-purity, high-strength cast Al-Cu alloy, which also has good plasticity and good welding and cutting performance, but poor casting performance. It is suitable for casting structural parts with large loads, such as support seats, arms and other parts. Sand and low-pressure casting are mostly used.
ZL205A: This is the highest strength aluminium alloy in the world. It has good plasticity and corrosion resistance, excellent cutting and welding performance, but poor casting performance. It is suitable for casting structural parts that bear heavy loads and some parts that do not require high air tightness. It is mainly made of sand casting, low-pressure casting, and metal casting.
ZL207 has high temperature strength. Its casting performance is average, and its welding and cutting performance is also average, but its room temperature strength is not high. It is suitable for various structural parts that work at a casting temperature of below 400°C, such as valve housings on aircraft engines, and some heat-resistant components in the oil refining industry. Sand casting and low-pressure casting are mostly used.
The tensile strength, yield point and high temperature strength of ZL209 alloy are higher than those of ZL201A, and its welding and cutting performance are also better, but its casting performance and elongation are poor. It is suitable for casting various components that require wear resistance at higher temperatures, such as parts on internal combustion engines. Sand casting is mostly used.
ZL301: This is the most corrosion-resistant variety among the existing aluminum alloys. It has good cutting and welding performance, high strength, and good anodizing performance, but the casting process is complicated, the operation is troublesome, and the castings are prone to defects such as looseness and thermal cracking. It is suitable for casting various parts with large loads in corrosive media such as seawater at a working temperature of 150°C, such as various components in marine ship casseroles, pump housings, impellers, frames and other parts in the petroleum industry, and mostly uses sand casting.
ZL303: Better high temperature strength than ZL301, good corrosion resistance (slightly worse than ZL301), superior cutting performance, good welding performance, better casting performance than ZL301, cannot be heat treated, making the mechanical properties much lower than ZL301. Suitable for casting parts such as aircraft engines, missiles, internal combustion engines, chemical pumps, oil pumps, petrochemical gas pump housings, rotors, blades, etc. that bear medium loads in corrosive media such as seawater, chemicals, and gas. Mainly used for pressure casting and sand casting.
ZL305: ZL305 due to the addition of Zn, reduce the content of Mg, casting performance and natural aging after the organisational stability are better than ZL301 and ZL303 alloy, the formation of loose, thermal cracking tendency is small. And because of the addition of Ti, Be two trace elements, suitable for the comprehensive performance of the alloy is good, strong resistance to stress corrosion, but poor mechanical properties at high temperatures. Suitable for casting to withstand a greater load in the sea water, chemical, gas and other corrosive media below 100 ℃ work in the aircraft, internal combustion engines, chemical pumps, oil pumps, petrochemical pumps, pump shells, rotors, blades and other parts. Mainly sand casting.
ZL401:ZL401 casting performance is very good, shrinkage and thermal cracking tendency is small, have high mechanical properties, welding and cutting performance is good, but the specific gravity, low plasticity, corrosion resistance is poor. Used as die casting and moulds, templates and working temperature does not exceed 200 ℃, bear medium load of aircraft, internal combustion engines, vehicles and other products on the structural parts. Mainly with pressure casting, also with sand and metal casting.
Comments are closed