Learn More About Heat Treatment For Steels
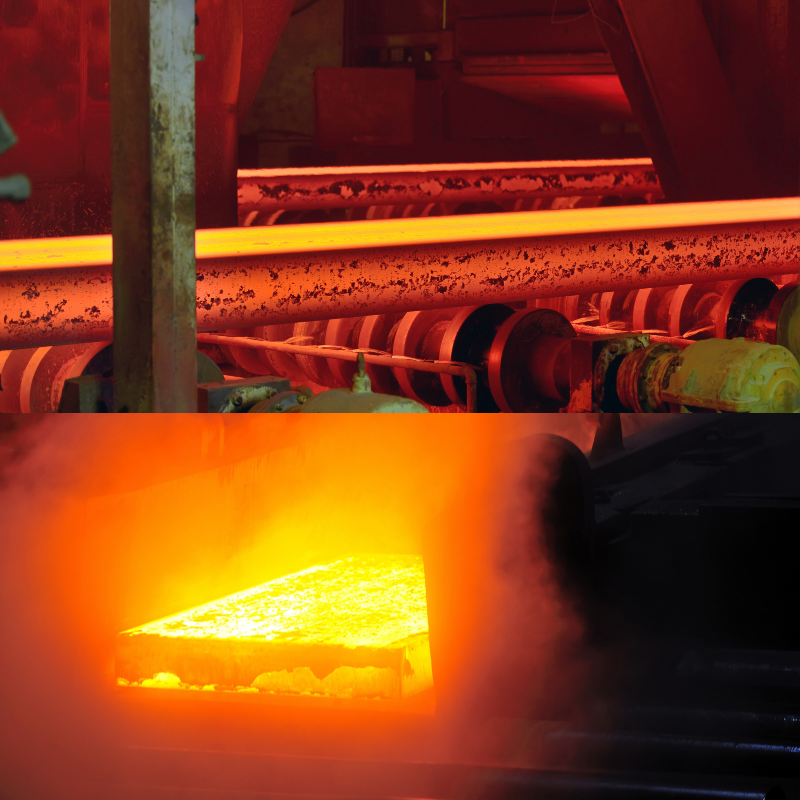
Heat treatment of steel refers to the heating, holding, cooling operations, so that the organisational structure of the steel changes to obtain the required properties of the process. Heat treatment process does not change the chemical composition and shape of steel, its purpose is:
- to improve the strength of parts, hardness and surface wear resistance;
- to eliminate residual internal stresses within the parts;
- to reduce the hardness of the parts to improve their machinability;
- to meet the corrosion protection and some other special requirements.
Therefore, the heat treatment process is widely used in precision machinery, some important parts such as gears, spindles. spring, as well as tools, moulds and gauges, etc., in the process of processing are required to be heat-treated in order to use. The insulation, cooling conditions and the different performance requirements of steel according to the heating, steel heat treatment mainly has the following types.
(1) Annealing: steel heated to the critical temperature above 20 ~ 30 ℃, after a certain period of time hold, followed by slow cooling, such a heat treatment process is called annealing. The purpose of annealing is to reduce the hardness of steel, improve machinability; refine the grain, reduce organisational heterogeneity, improve the toughness and plasticity of steel; eliminate residual stresses, to prevent deformation and cracking of steel.
(2) Normalising: the steel heated to the critical temperature above 30 ~ 50 ℃, after a certain period of time insulation, and then cooled in the air heat treatment method known as normalising. The cooling rate of normalising is faster than annealing, the heating and holding time is the same, so you can get a finer organisation than after annealing, which results in higher mechanical properties, hardness and strength than after annealing.
(3) Quenching: Quenching, also known as hardening, refers to the heating of steel to a critical temperature above 30 ~ 50 ℃, holding time, and then in water, brine or oil in the rapid cooling. The purpose of quenching is to improve the hardness and wear resistance of parts. Because the quenched material is hard and brittle, and internal stress, so the quenched parts cannot be directly applied, it must to be tempered.
4) Tempering: the quenched parts reheated to a temperature below the critical temperature, hold for a certain period of time, and then in the air, water or oil cooling process known as tempering. The purpose of tempering is to eliminate the internal stresses caused by rapid cooling during quenching, reduce the brittleness of steel, so that it has a certain toughness. Thus, tempering is not an independent process, it is the process must be carried out after quenching. Tempering can be divided into low-temperature tempering, medium temperature tempering and high temperature tempering according to different heating temperatures.
(1) Low-temperature tempering heating temperature of 150 ~ 250 ℃, its purpose is to maintain high hardness of the material under the premise of reducing its quenching stress and brittleness, for the need for high hardness (59 ~ 62HRC) of the tool and will be subjected to strong friction parts, such as cutting tools, moulds and rolling bearings.
(2) Medium temperature tempering heating temperature of 300 ~ 450 ℃, its purpose is to eliminate the internal stress after quenching, to obtain high elasticity, a certain degree of hardness and toughness, for the need for good elasticity, a certain degree of hardness (35 ~ 45HRC) and a certain degree of toughness of parts, such as springs, hot pressing moulds and other parts.
(3) High-temperature tempering heating temperature of 500 ~ 650 ℃, the purpose is to eliminate the internal stress after quenching, to obtain higher toughness and ductility, but the lower hardness (200 ~ 350HBS) is lower after high-temperature tempering of the parts, Usually after quenching by high temperature tempering heat treatment process called tempering treatment. Some important parts, such as spindles, connecting rods, screws, gears, etc. need to be tempered. Compared with normalised steel, tempered steel is not only stronger, but also tougher and more ductile, so it is the most widely used heat treatment process.
5) Surface quenching: surface quenching is mainly by combined with rapid heating and immediate quenching and cooling to achieve so that the surface of the steel parts quickly reaches the quenching temperature, and then do not wait for the heat to the centre, that is, to be rapidly cooled, the result is only to make the surface layer is quenched, and the centre is still retained in the original ductility and toughness of the annealed, normalised or tempered state of the organisation. Surface hardening is generally applicable to parts requiring high surface hardness and high internal toughness, such as gears, worms, screws and journals. The main surface quenching can have as follow according to the different methods of heating: induction heating (high frequency, medium frequency, industrial frequency), flame heating, electric contact heating and electrolyte heating surface quenching.
(6) Chemical heat treatment chemical heat treatment refers to the workpiece placed in a certain medium heating and insulation, so that the medium of the active atoms penetrate the surface layer of the workpiece to change the chemical composition and organization of the surface layer, so that the surface of the workpiece has a particular mechanical, physical or chemical properties. Chemical heat treatment process more, infiltration of different elements, will make the surface of the workpiece has different properties. The following three common.
(1) Carburizing Carburizing is the process of infiltrating carbon atoms into the surface layer of steel. Its purpose is to make the surface of the workpiece after heat treatment with high hardness and wear resistance, while the core still maintains a certain strength, high toughness and ductility. According to the use of different carburizing agents, carburizing method can be divided into gas carburizing, solid carburizing, liquid carburizing three. Carburizing is generally mainly used for low carbon steel, low carbon alloy steel workpiece. For some gears, shafts, piston pins, universal couplings and other requirements of the surface layer of hardness, wear resistance, fatigue strength, core toughness and ductility are very high load parts, carburizing also need to be quenched and low-temperature tempering
(2) Nitriding: Nitriding is the process of infiltration of nitrogen atoms into the surface layer of the steel parts. Nitriding temperature is generally low, usually lower than the tempering temperature of the tempering treatment. The deformation of the parts in the nitriding process is small, the fatigue strength of the parts after nitriding is high, and a dense nitride layer can be generated on the surface, which has good corrosion resistance. Nitriding can obtain than carburizing quenching higher surface hardness, wear resistance, hot hardness, fatigue strength and better corrosion resistance, nitriding does not need to be quenched. Nitriding is mainly used for high hardness and wear resistance, as well as not easy to grind precision parts, such as gears (especially internal gears) spindles, mantis rod, precision screws, gauges, Molds and so on.
(3) Cyanide: Cyanide is to infiltrate carbon and nitrogen into the surface layer of the parts at the same time, so it is also known as carbon and nitrogen co-infiltration. Cyanide treatment can improve the hardness, corrosion resistance and fatigue strength of the surface of the parts, and maintain the toughness and ductility of the core of the parts. At present, low-temperature (<570 ℃) cyanide treatment (also known as gas nitrocarburizing) and medium-temperature (700 ~ 800 ℃) cyanide treatment is more widely used.
Comments are closed